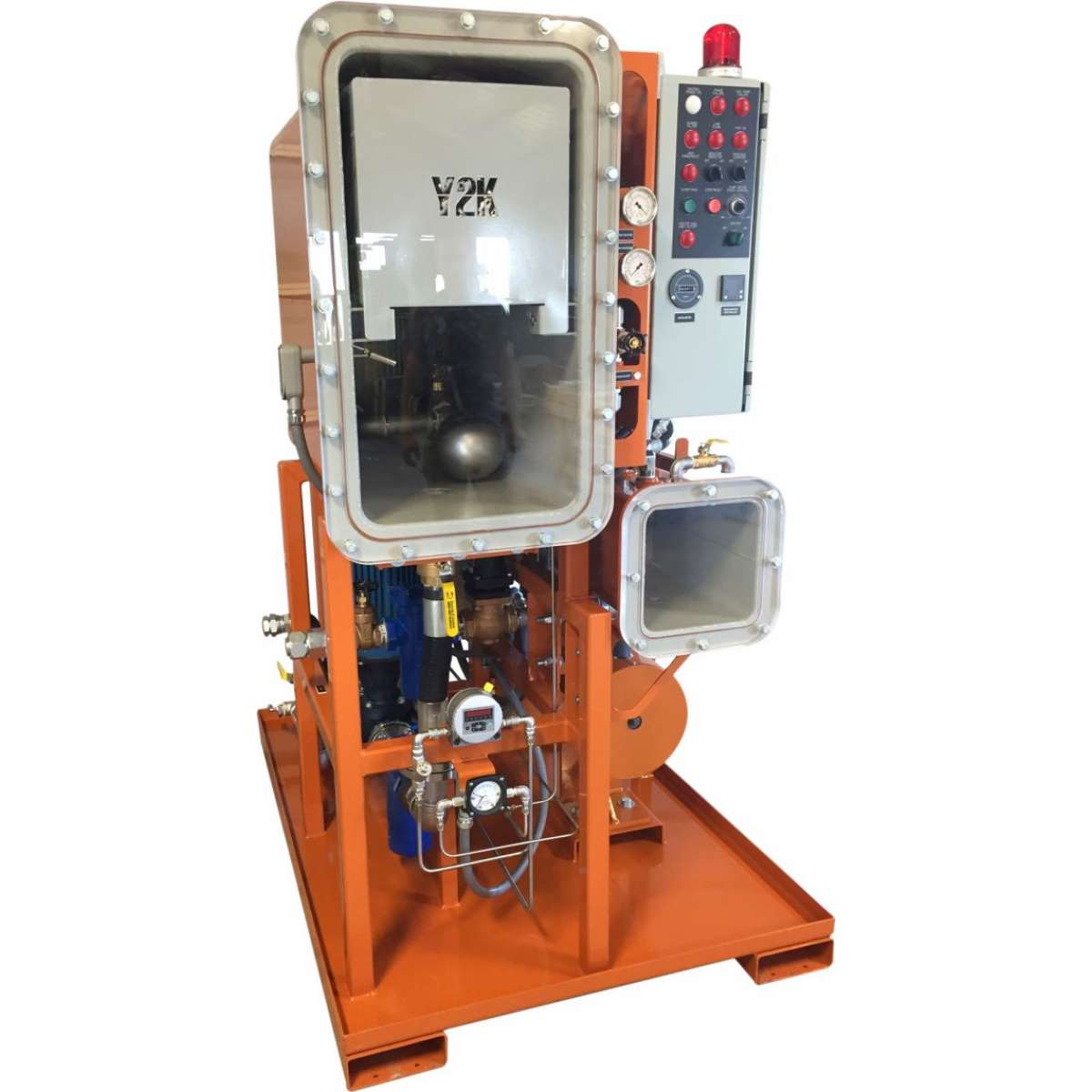
Lubrigard 50 GPM Vacuum Dehydration 480V/3P/60Hz

Vacuum Dehydration System
The purpose of the FD-5 Vacuum Dehydration System is to serve as an oil treatment system. By removing water (dissolved, emulsified and free), gasses and solid contaminants the oil can return to its original condition, and be reused in lubricating systems. Having clean, dry oil will allow hydraulic and lubricating systems to perform more efficiently and can result in significant financial gains. The need to purchase new lubricating oils can be reduced and in some cases eliminated completely.
To begin, the oil is brought into the chamber and passed over the heater and heated. It then is dispersed over the Pall Rings , located inside the tower, and then exposed to a vacuum, usually between 22-25"Hg.
After the oil has been degassed and dehydrated it is pumped out of the bottom of the tower via the hydraulic pump into the filter to remove any contaminants before it enters the reservoir or system again.
In order to optimize this process the FD-5 Purifier is partially automated with a PLC and series of electrically controlled switches. Data, diagnostics, alerts and many help screens can be accessed on the control panel touch screen display.
Typical Applications:
- Filtering Pulp and Paper lube systems
- Filtering steam turbine lube systems
- Filtering hydraulic reservoirs
- Filtering rolling mill lube tanks
- And many other industrial applications containing oil
Typical Industries:
- Power Generation
- Mining
- Pulp and Paper
- Steel
- Automotive Manufacturing
- Water and Particulate Removal System - 50 GPM- 7 (NEMA 7 Rated)
- Class 1, Div. 2, Groups B,C&D hazardous locations
- Flow Rate - 50 GPM
- Pre-Filtration -(Inlet BASKET Strainer 20 Mesh)
- Filtration - Equipped With An Industry Standard Absolute Rated Micro-Glass Filter Element In A Hydraulic Filter Housing Rated to 150 PSI maximum pressure
- Heater - 66 kW Single Circulation 2 Circuit Low Watt Density Heater NEMA 4/7 rated
- Inlet/Discharge Size and Connections - 2" JIC
- Heat exchanger -Electric Air Cooled
- Pre-Filtration (Discharge Pump)- (Inlet BASKET Strainer 20 Mesh)
- Discharge Pump - Internal Gear w/Pressure Relief Set@ 100 PSI
- Discharge Pump drive motor - 480V/ 3 Ph/ 60 Hz TEFC. NEMA 7 Class I Div. 2 Rated
- Base - Carbon Steel With 2.0" Spill Containment Rail, Fork Slots, And Low Point Drain
- Caster mount holes
- Vacuum System - Claw Style Type 106 CFM @ 3450 RPM Ultimate Vacuum 28.44 (In.Hg), Ultimate Vacuum
- Continuous Operation 27 (In. Hg) with NEMA 7 Class I Div. 2 rated motor
- Oil Sampling Ports- " Best Practice" Quick connect with dust caps
- Instrumentation - Liquid Filled Industrial Style Panel Mount
- Inlet Safety Direct Acting Solenoid Valve - 120 V/ 1Ph/ 60 Hz. NEMA 7 Rated
- Safety Discharge Check Valve - Inline Ball Style 5 PSI Cracking Pressure
- Piping - 304SS, Rated For Temperature To 225 deg. F. @ Pressures Rated To 150 PSI
- Paint - Industrial Type Primer And Corrosion Resistant Finish
- Internal Coating - Dry Powder Fusion Bonded Industrial Powdered Coating
- Control Panel - NEMA 7 Rated Equipped with, Industrial Grade NEMA 7 rated Pilot Lights, Variable Frequency Drive (VFD), and PLC
- Temperature/ Hour meter NEMA 7 Enclosure- NEMA 7 rated port hole housing to contain The digital temperature controller, and hour meter
- System Voltage - 480V 3 Phase 60 Hz (100 AMP)
- Dimensions - 54"W X 80"L X 85"H Estimated
- Weight-Estimated 4,200 Lbs.
- 26 WEEK LEAD TIME
Operator Interface Panel Features:
- One button start/stop
- Unattended operation
- Automatic PLC based controls safely monitor the system and will shut it down if operating parameters move outside normal limits
- Touchscreen Panel displays all conditions, including possible causes and remedies
- Troubleshooting and help screens
Contaminant | Type FD-15 Capability |
---|---|
Water Remove | 100% free water plus 90% dissolved water |
Particulate | ISO Cleanliness Code 13/11/8; per ISO 4406:1999 |
Gasses | Remove 100% free gases plus 90% dissolved gases |
Air | Remove 100% free air plus 90% dissolved air |