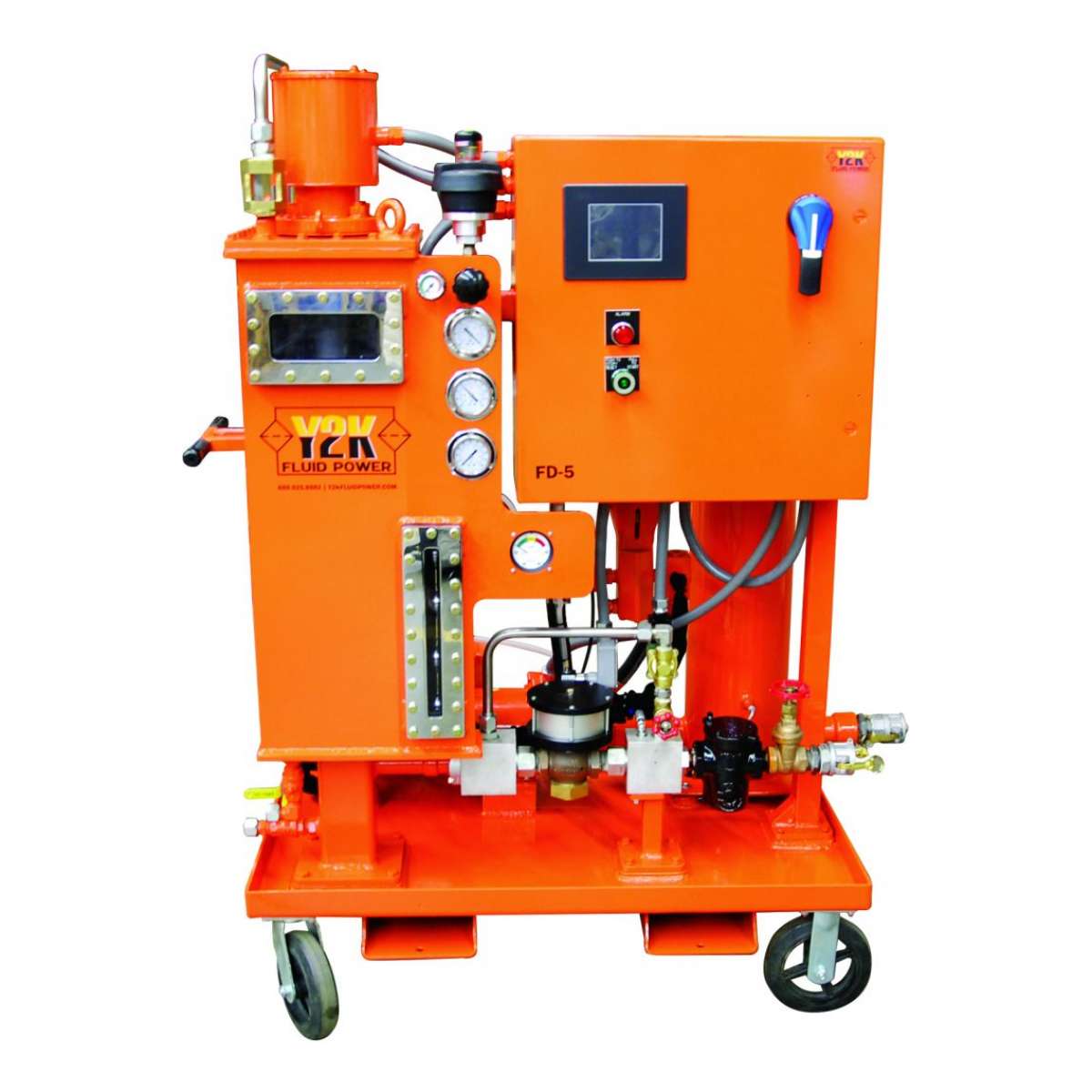
Lubrigard VACUUM DEHYDRATION UNIT - 5 GPM

Vacuum Dehydration System
The purpose of the FD-5 Vacuum Dehydration System is to serve as an oil treatment system. By removing water (dissolved, emulsified and free), gasses and solid contaminants the oil can return to its original condition, and be reused in lubricating systems. Having clean, dry oil will allow hydraulic and lubricating systems to perform more efficiently and can result in significant financial gains. The need to purchase new lubricating oils can be reduced and in some cases eliminated completely.
To begin, the oil is brought into the chamber and passed over the heater and heated. It then is dispersed over the Pall Rings , located inside the tower, and then exposed to a vacuum, usually between 22-25"Hg.
After the oil has been degassed and dehydrated it is pumped out of the bottom of the tower via the hydraulic pump into the filter to remove any contaminants before it enters the reservoir or system again.
In order to optimize this process the FD-5 Purifier is partially automated with a PLC and series of electrically controlled switches. Data, diagnostics, alerts and many help screens can be accessed on the control panel touch screen display.
Typical Applications:
- Filtering Pulp and Paper lube systems
- Filtering steam turbine lube systems
- Filtering hydraulic reservoirs
- Filtering rolling mill lube tanks
- And many other industrial applications containing oil
Typical Industries:
- Power Generation
- Mining
- Pulp and Paper
- Steel
- Automotive Manufacturing
Flow Rate: | 5 GPM |
Vacuum Pump Flow Rate: | 13 CFM |
Heater Capacity: | 3KW @ 15wsi |
Motors: | 3 HP, 480 VAC, 3 Phase; Other voltages are available |
Plumbing Requirements: | Inlet: 1 1/2" FNPT; Outlet: 1 1/2" FNPT |
Approximate Dry Weight: | 950 lbs |
Dimensions: | 44"L x 30.5"W x 68"H |
Start Up Bypass: | Standard |
Condenser: | Optional |
Water Monitor: | Standard |
Chamber: | Pall Dispersion Rings |
Chamber Vaccum: | 22-27" Hg |
Fluid Temperature: | Adjustable heater up to 180°F. Factory set at 145°F and is customer adjustable up to 165°F |
Filtration: | Highly efficient ß1000 filter element. Micron sizes range from 1UM to 25UM |
Seal Material (s): | Buna N, Viton, EPDM or EPR |
Max Fluid Viscosity: | ISO 680 or 4250 SUS |
Inlet Pressure Maximums: | 10" Hg Vacuum to 15psig |
Outlet Pressure Maximums: | 65psig Max |
Continuous Heater Flow: | Minimum 2-6 GPM continuous flow through heater to prevent oil coking |
Console Remote Alarm: | 250 V, 10 AMP dry contact rating |
Wheel Configuration: | Caster wheels, pneumatic tires, fork lift pockets or floor mount |
Water Removal Rate: | Removal rate of water will vary depending on fluid properties and application parameters |
Operator Interface Panel Features:
- One button start/stop
- Unattended operation
- Automatic PLC based controls safely monitor the system and will shut it down if operating parameters move outside normal limits
- Touchscreen Panel displays all conditions, including possible causes and remedies
- Troubleshooting and help screens
Contaminant | Type FD-15 Capability |
---|---|
Water Remove | 100% free water plus 90% dissolved water |
Particulate | ISO Cleanliness Code 13/11/8; per ISO 4406:1999 |
Gasses | Remove 100% free gases plus 90% dissolved gases |
Air | Remove 100% free air plus 90% dissolved air |